How Welding Inspection Madison Makes Sure Top Quality and Safety in Fabrication
How Welding Inspection Madison Makes Sure Top Quality and Safety in Fabrication
Blog Article
Exploring Advanced Equipment and Techniques for Accurate Welding Inspection
In the realm of welding examination, the search of precision and reliability is critical, stimulating the advancement of advanced devices and methods. Laser scanning developments and computerized assessment systems, geared up with man-made intelligence, are redefining the landscape by minimizing human mistake and enhancing security steps.
Ultrasonic Testing Advancements
Ultrasonic testing advancements regularly represent the leading edge of innovations in welding evaluation modern technologies. These advancements have considerably enhanced the capability to spot and evaluate discontinuities within bonded frameworks, making sure enhanced stability and safety.
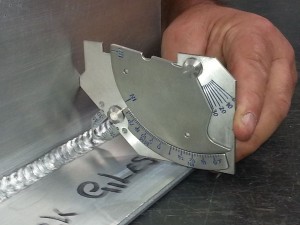
In addition, advancements in software application algorithms for information evaluation have actually enhanced the precision of problem discovery and sizing. Automated ultrasonic testing systems currently provide high-resolution imaging, enabling detailed evaluations of weld high quality. These systems are often integrated with sophisticated visualization tools, which facilitate the interpretation of results.
Radiographic Inspection Strategies
While ultrasonic screening developments have actually established a high criterion in non-destructive evaluation, radiographic assessment methods remain to play an essential function in welding evaluation by supplying distinct understandings into material honesty. Radiographic testing (RT) uses making use of X-rays or gamma rays to pass through materials, developing a radiograph that visually stands for the inner framework of a weld. This imaging capability is very useful for discovering subsurface problems such as porosity, inclusions, and splits that might not show up through surface area evaluations.
The procedure entails placing a radiation resource on one side of the weld and a detector on the opposite side. Variants in material density and thickness influence the attenuation of the rays, generating a contrasting photo that exactly marks defects. RT is particularly beneficial for checking thick areas and complicated geometries where other approaches might drop brief.
In spite of its performance, radiographic examination has to be performed with rigorous adherence to safety and security protocols due to the unsafe nature of ionizing radiation. Furthermore, the analysis of radiographs needs competent personnel, as the top quality of the analysis directly impacts the dependability of the assessment. As a result, continuous advancements in digital radiography are improving image clearness and interpretation effectiveness, enhancing RT's crucial duty in making certain weld top quality.
Laser Scanning Advances
Embracing laser scanning modern technology in welding examination has changed the evaluation of weld quality and integrity. This advanced technique uses a non-contact, high-resolution means of catching thorough 3D data of weld surfaces. Unlike conventional assessment techniques, laser scanning gives fast information purchase, substantially enhancing the performance and accuracy of weld examinations. The modern technology employs laser light beams to produce precise 3D designs, which are important for in-depth analysis of weld dimensions, surface area irregularities, and prospective flaws.
Laser scanning advancements have caused significant enhancements in discovering and identifying surface imperfections such as porosity, lack of fusion, and undercuts. The high-resolution information enables examiners to perform detailed analyses, ensuring that welds satisfy rigid sector requirements. Furthermore, this technique sustains the advancement of electronic records, helping with lasting top quality guarantee and traceability.
Additionally, laser scanning modern technology integrates effortlessly with software application services made for automated problem discovery and evaluation. The resultant data can be conveniently shared and evaluated, promoting joint decision-making procedures. As sectors continue to require higher criteria for weld quality, laser scanning continues to be at the forefront, using unrivaled accuracy and effectiveness in welding have a peek at this site evaluation.
Automated Inspection Solutions

Automated examination systems offer the advantage of consistency, getting rid of human error and subjectivity from the assessment process. They are developed to operate in numerous environments, from manufacturing floorings to remote field websites, making certain comprehensive coverage. Welding Inspection Madison. These systems can be set to comply with certain welding requirements and criteria, offering thorough reports and paperwork for high quality control purposes
Moreover, the assimilation of cloud-based systems helps with the storage space and evaluation of huge quantities of inspection data. This makes it possible for pattern evaluation and anticipating upkeep, permitting suppliers to deal with prospective problems before they escalate. The adoption of computerized examination systems is a crucial move in the direction of boosting the reliability and effectiveness of welding procedures in industrial applications.
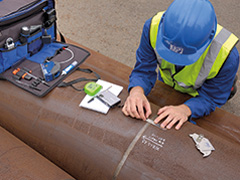
Enhancing Security and Effectiveness
A substantial facet of boosting security and performance in welding assessment hinges on the combination of cutting-edge technologies that simplify operations and minimize dangers. The fostering of innovative non-destructive screening (NDT) methods, such as ultrasonic screening, phased array ultrasonic screening (PAUT), and radiographic testing, plays an essential role in making sure architectural integrity without compromising the security of the employees entailed. These methods enable for thorough examinations with minimal downtime, lowering possible dangers connected with typical approaches.
Moreover, the implementation of real-time information analytics and artificial intelligence algorithms has changed the means examination information is analyzed. By using predictive analytics, prospective problems can be identified prior to they manifest into important failures, making sure prompt treatments and maintenance. This aggressive strategy significantly boosts operational performance and safety in welding processes.
Furthermore, remote examination technologies, consisting of drones and robotic spiders equipped with high-resolution electronic cameras, make it possible for inspectors to examine hard-to-reach locations without subjecting them to dangerous problems. This not just enhances assessment accuracy but likewise decreases human risk. By leveraging these innovative tools and methods, sectors can achieve greater security standards and operational efficiency, eventually leading to more reliable and lasting welding evaluation methods.
Final Thought
The combination of advanced devices and techniques in welding assessment dramatically boosts defect detection and ensures structural honesty. Welding Inspection Madison. Advancements such as phased array ultrasonic screening, digital radiography, and laser scanning boost issue characterization, while automated examination systems and AI decrease human error. Remote modern technologies assist in risk-free assessments in harmful atmospheres, advertising a positive maintenance technique. These innovations not just increase evaluation effectiveness yet likewise add to boosted security and quality assurance in continue reading this industrial welding applications.

Ultrasonic testing technologies often represent the center of innovations in welding inspection innovations.While ultrasonic screening technologies have set a high requirement in non-destructive evaluation, radiographic inspection strategies continue to play an integral duty in welding inspection by supplying one-of-a-kind understandings right into product stability.Welcoming laser check my site scanning innovation in welding inspection has revolutionized the evaluation of weld high quality and integrity. As industries proceed to demand higher requirements for weld high quality, laser scanning stays at the forefront, supplying unmatched accuracy and performance in welding examination.
Automated inspection systems supply the advantage of consistency, getting rid of human mistake and subjectivity from the inspection process.
Report this page